CabParts Online FAQs
Frequently Asked Questions
Do you have a question?
Below you’ll find the answers to our most common online questions. If you can’t find an answer, please contact us.
Answer: YES, to all three. When CabParts began, we were held to drilling based upon increments of 32mm. With our modern CNC machinery, that is no longer required. Rather than a single line of holes for hinges, slides, and shelves, they are now separated and you no longer have to count holes to locate your hardware.
Hinge plates remain at 37mm back, but hinge plates (and cups) are equally spaced from the tops and bottoms of the doors (the default is 3”). Drawer slide holes are placed according to the hardware/pattern you select, while shelf holes move to 52mm back.
Locations are obvious and installation becomes significantly faster and less susceptible to error.
For example, I want to use a Wilsonart laminate on my doors, drawer fronts, and finished end panels but do not see it listed as an option?
Answer: For any materials not listed, including laminates, look for “Custom” in the drop-down lists. Selecting “Custom” will give you the choices of up to 3 grained materials, 3 non-grained materials, or 6 edgebands. Assign each of your special materials or bandings to one of those selections. CabParts
Online will use the custom items selected and give you a “high average” pricing only as a place-holder. In the Notes section of the order, in the separate CabParts Online “Custom Materials Order Form”, or in an email or FAX, let us know what each of those Custom materials represents. Submit the order. We will check on price and availability and then adjust the pricing for you, up or down. That adjustment will be reflected in the job confirmation email we send you after you submit your order.
For example, I want to remove the dado and back altogether, or extend the right side up and the left side down, or I want to drill for pulls or locks, but those options are not available?
Answer: First, DO NOT try to use the line-item Notes to modify a cabinet – those notes do not affect the cabinet and its construction in any way. They are for information only. CabParts Online does a lot, and will do more in the future, but it will never do everything! We will always want to be your go-to custom shop and the solution here is to use an alternate system when CabParts Online will not work.
We suggest you use CabParts Online for what it can do, and for those really special or custom items, use the Custom Order form. It is a separate form, essentially the paper order form we have used for many years but modified for this purpose. You can also use our existing PDF Drop-Down order form.
We will prepare an estimate for your approval after we receive the “paper” order.
The non-Online part of your order will be handled as a separate job. If it is part of an online order, it will have the same Order Number with the Add-on noted, for example “Order # 856-A1”.
The custom unit(s) will slow the process, so let us know if you want everything shipped at one time or
separately as soon as completed.
For example, I have a kitchen with cabinets along the walls finished with one color, an island in another color (but both with prefinished maple interiors) and a laundry with white interior and white laminate doors?
Answer: Do each variation as a separate order and label each (Project and Phase) accordingly. Generally, as best practice, you will want to do a new order (call it a sub-order?) each time you change main case materials or edgebanding. For this example, Project could be “Jones Home Remodel Job
1234” and Phase is “Kitchen Perimeter”, “Kitchen Island”, “Laundry”, etc. This is actually faster (and easier to keep track of) than going into the Configurator and changing a few (or many) cabinets here and there.
For example, my billing and shipping addresses are always the same and I almost always order white melamine cabinet boxes with no doors, drawer fronts, drawer boxes, slides, or hinges?
Answer: After you enter all of the repetitive information in an order form, use the “Save as New Order” command (in the status drop-down menu) to save the job as a template. Call it a “Template” in the new copy, in the Project (or Phase) labels. Then, to enter a new job, locate and load the Template
“order”, save it as a new order, and then use the resulting new order, with its’ new order number, to enter your actual job. As long as you do not change the Template it will be available to copy and use as many times as you like.
For example, I need a tall cabinet with an open bay on the top (no doors and finished interior), a bay with drawers in the middle and a bay with doors on the bottom – I do not see that in the catalog?
Answer: Stack existing catalog units, for example, existing base units. If you do not want to see a seam, add a plant-on finished side panel. Your installers – who will be able to carry these smaller and lighter stackable units, instead of one large, heavy, and awkward tall cabinet, up one or two flights of
stairs – will love you. You can see examples of stacking in the Cabinet Defaults tables. Alternatively, if stacking will not work, you can use the Custom unit/order system (costs more!)
For example, I have access to some very special materials and feel I can get a better price, but want CabParts to process them. I will pay to have them delivered to you.
Another example, CabParts already has some of our material in stock, left over from another job.
Answer: Remember that, if CabParts does not supply the material, you will be responsible for it arriving at our shop in time, in good condition and in enough quantity to do the job, including a bit extra to allow for any shipping damage and the like. Use the “Custom” option in CabParts Online for the material (and any edgebanding) you are supplying. We will use the Special-Order Price Worksheet to deduct the amounts for your materials. Processing
of your materials will still be included in the pricing of your order. You will need to let us know which “Custom” selection goes with which material or edgeband – in the
Notes in your order, using the “Custom Materials” form, or in separate correspondence
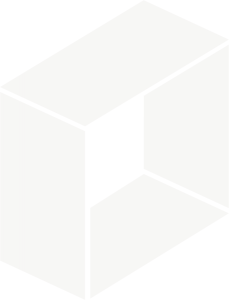